Introduction
My goal with this project was to create a wooden tongue drum decorated in computationally fabricated elements. A wooden tongue drum is usually a wooden box with tongue shapes cut out of the top that resonate at different freuquencies, yielding a playable instrument. I wanted to learn to use wood and the CNC milling machine in fabrication, and also ended up learning how to use the GlowForge laser printer with wood as well. I was inspired by the harmonic series, caustic networks (those flowing light patterns you see from light reflecting off undulating water), and sacred geometry.

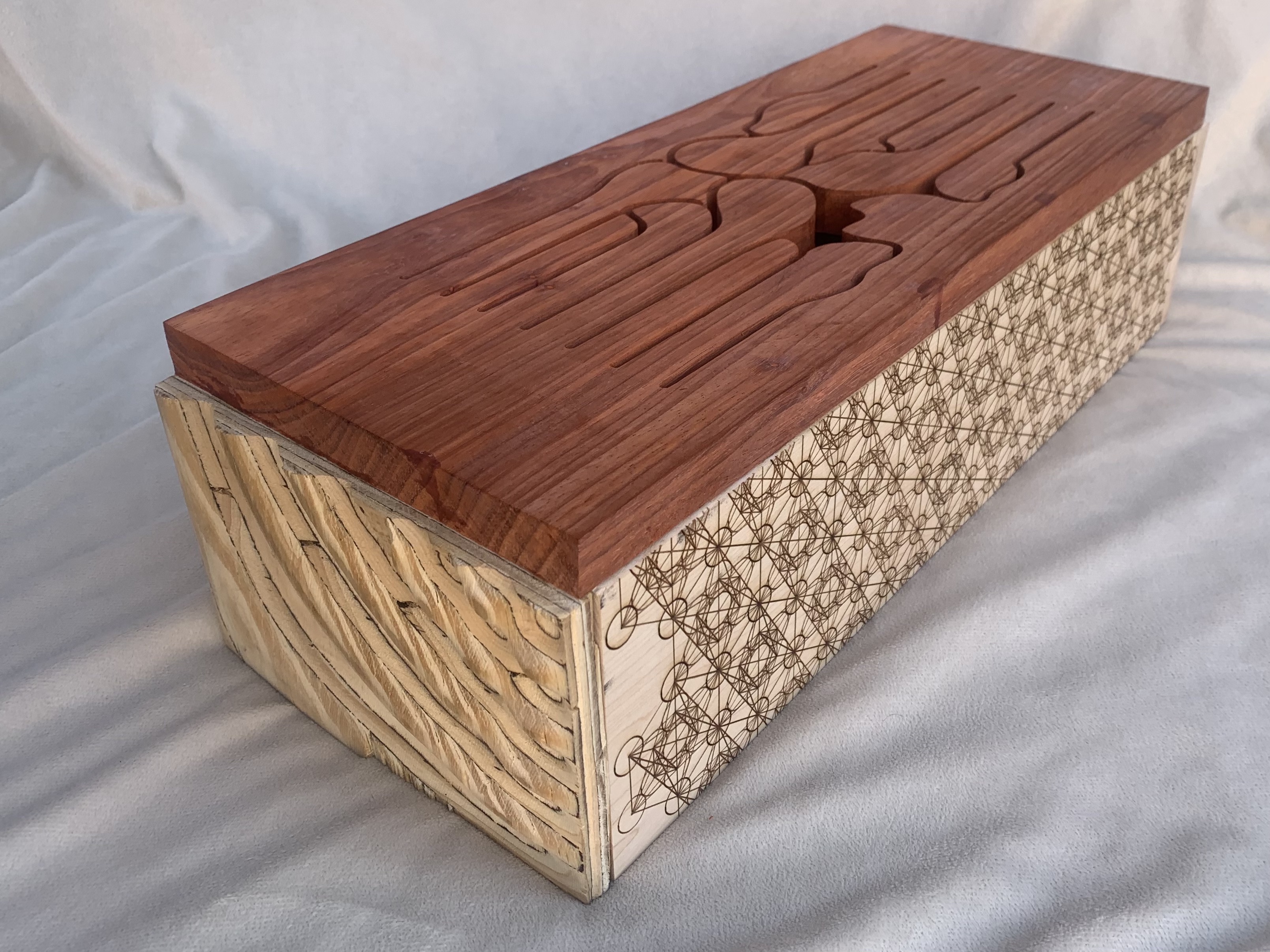
Related Works
https://www.cs.columbia.edu/~cxz/publications/metallophone.pdf
For designs on the sides, I am currently inspired by the works of Rebal Jaber, specifically Liquid Wood
https://www.rebaljber.com/work/liquid-wood
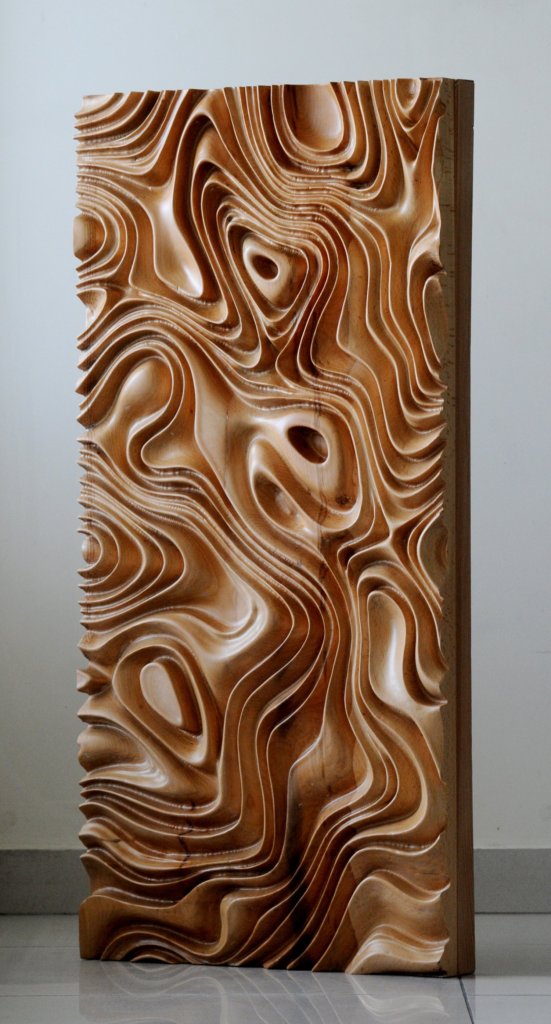
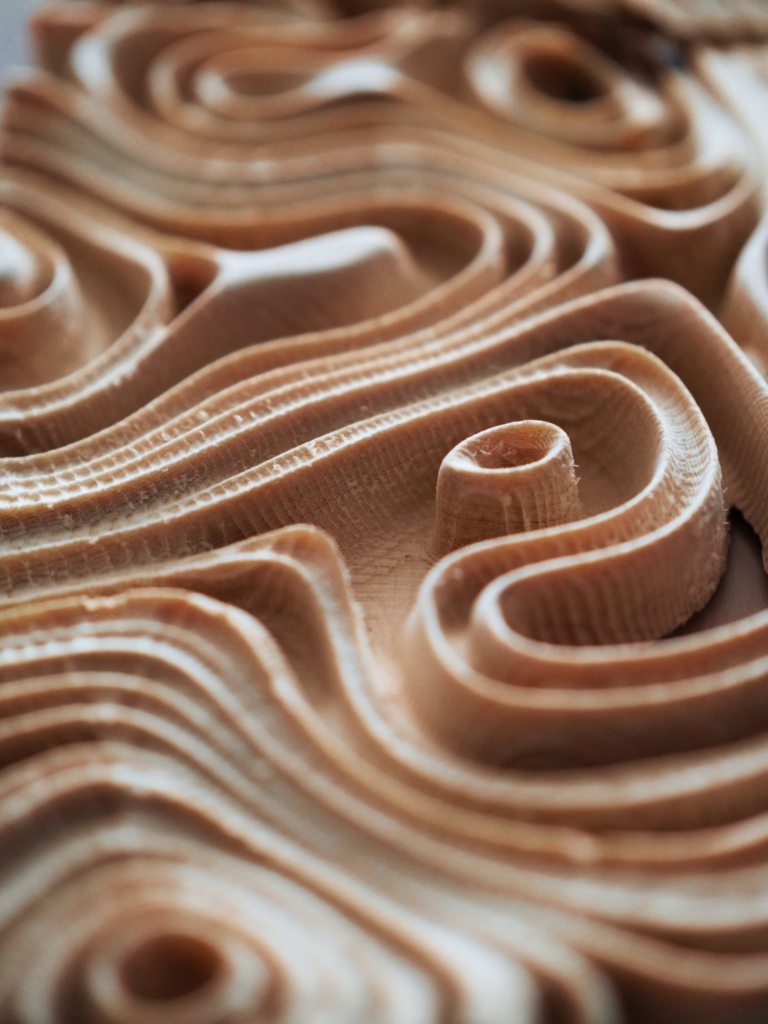
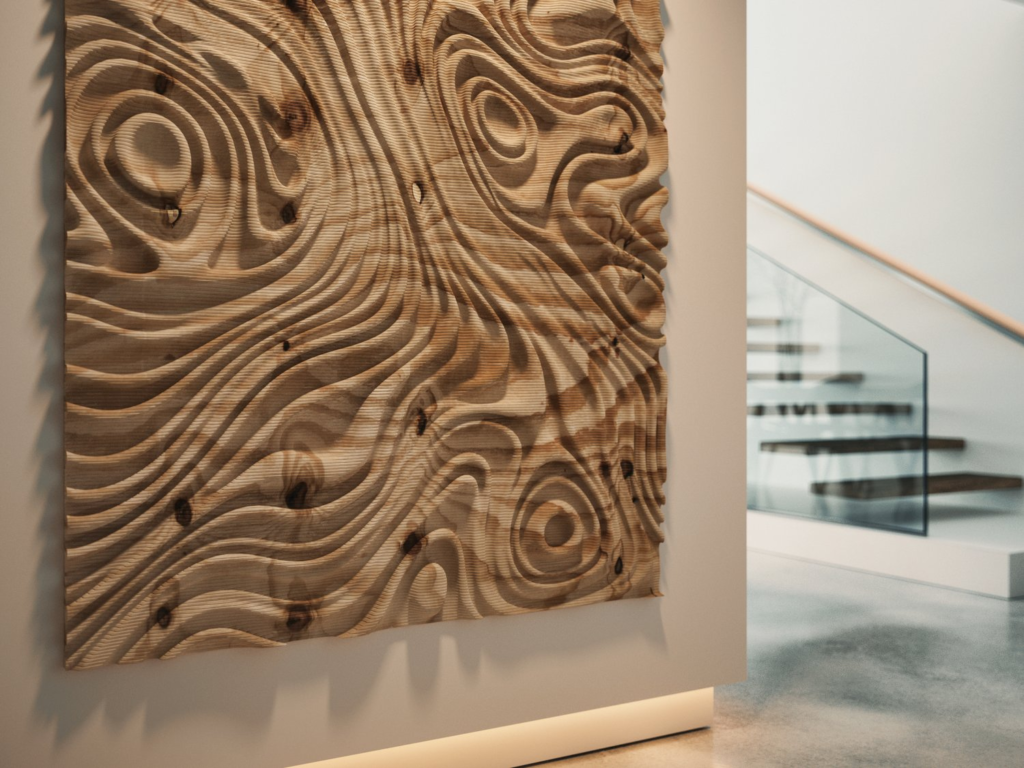
I am similarly inspired by the work of agatakycia, ISOpatterns
Another inspirations is of course, people who have built wooden tongue drums. This video is a particularly good video in which they also use a CNC machine for cutting the tongues, though the design was created in Illustrator rather than computationally generated.
Process
One of my programs represents the harmonic series. Sounds in nature don’t just produce one singular frequency (or pitch). They also produce harmonic frequencies, which have integer multiples of the frequency of the fundamental note – or the main note that we hear. Different harmonics (and inharmonics) are more pronounced by different instruments, which is why you can play the same notes on a piano, flute, and guitar, but they all have their own distinctive sound characteristics. The first overtone has twice the frequency of the fundamental, producing a note that is an octave higher. The second harmonic has 3x the frequency of the fundamental, providing the octave+fifth of the fundamental, etc. It’s a beautiful concept I wanted to model. I used a turtle to create the vertical sin waves and had the turtle move to the side for each wave, while also incrementing the number of oscillations. Then I was able to loft the waves together and make a model ready to import to the CNC software, Easel.
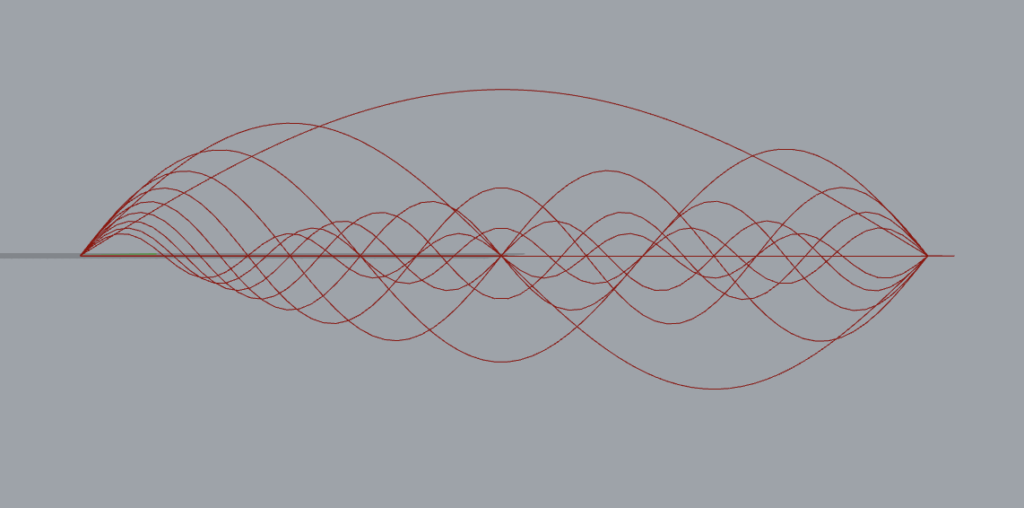

I used the CNC machine to carve this out of some cheap plywood. It worked pretty well, though I did notice that the material would splinter when the machine was cutting perpendicular to the grain of the wood. The CNC machine will can do two passes – a roughing pass to take out big chunks of wood, and a finishing pass with a smaller bit to get the details. Luckily for the finishing pass, I could change the tool paths to go in a certain direction to match the grain of the wood, which resulted in much less splintering and a cleaner finish. Another problem I had was that the roughing pass wanted to cut the whole model out, and so it separated the piece from the rest of the wood which made it not able to be clamped down anymore for the finishing pass. The separated piece was loose which is dangerous and the bit moved it around and sliced through it. I fixed this within the Easel software, which allowed me to tell the machine to only cut the material to a certain depth.
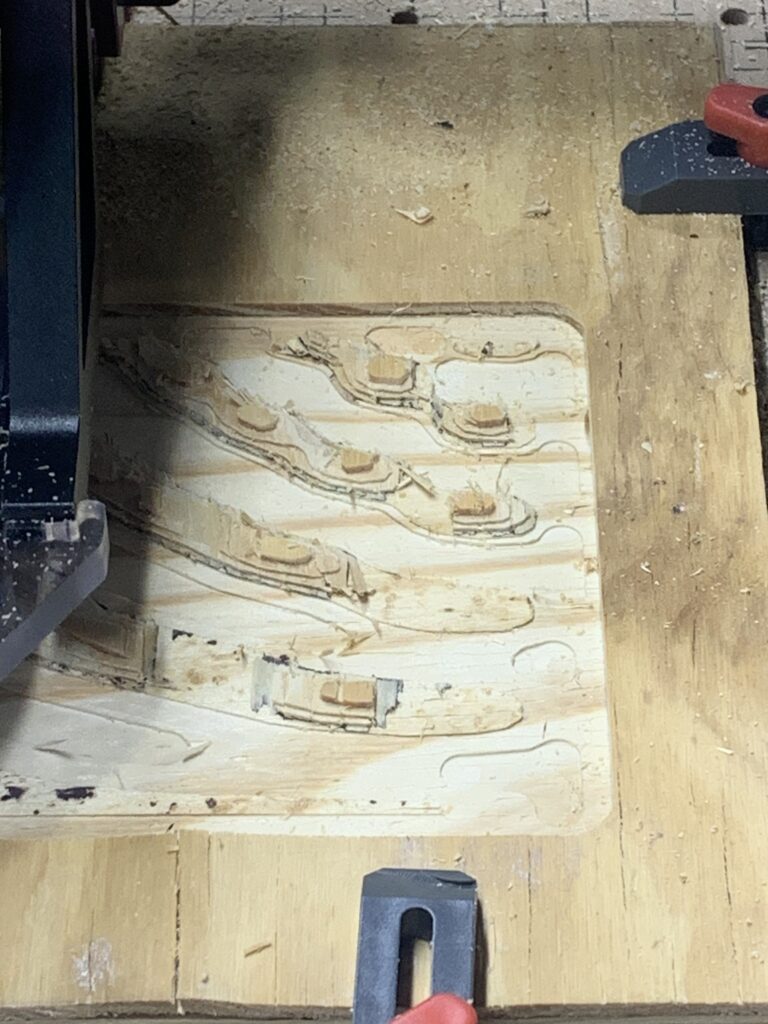

My other 3D program was inspired by caustic networks, and I wanted to emulate the flowing and undulating abstract patterns of light and water. I did something similar in which I created sin waves with turtles in which every other wave went either up or down first. Then I accesed the points on the wave lines and used rs.MoveObject(…) to move the points around in X Y and/or Z to make more interesting lines and undulations.
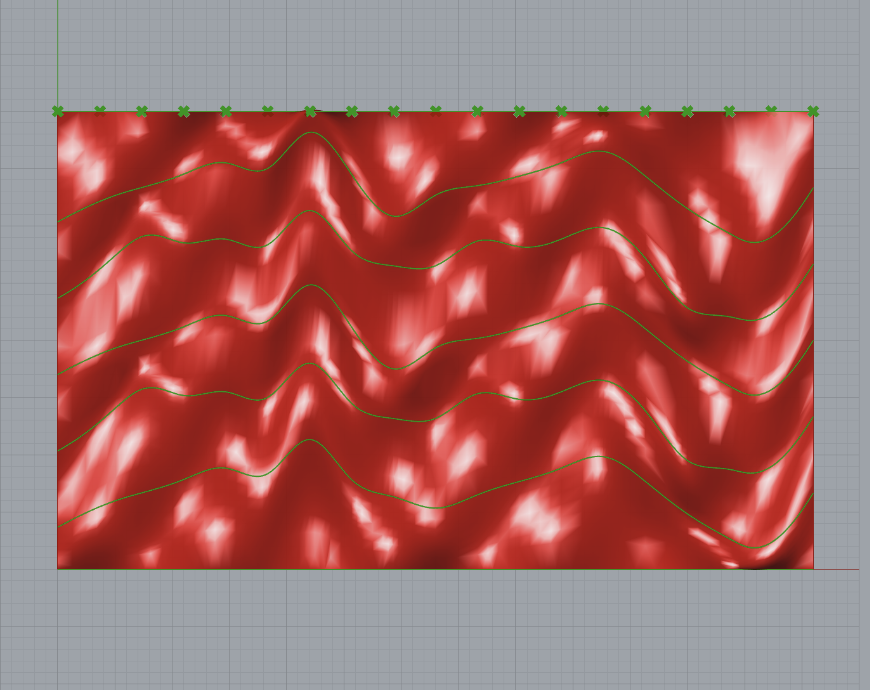
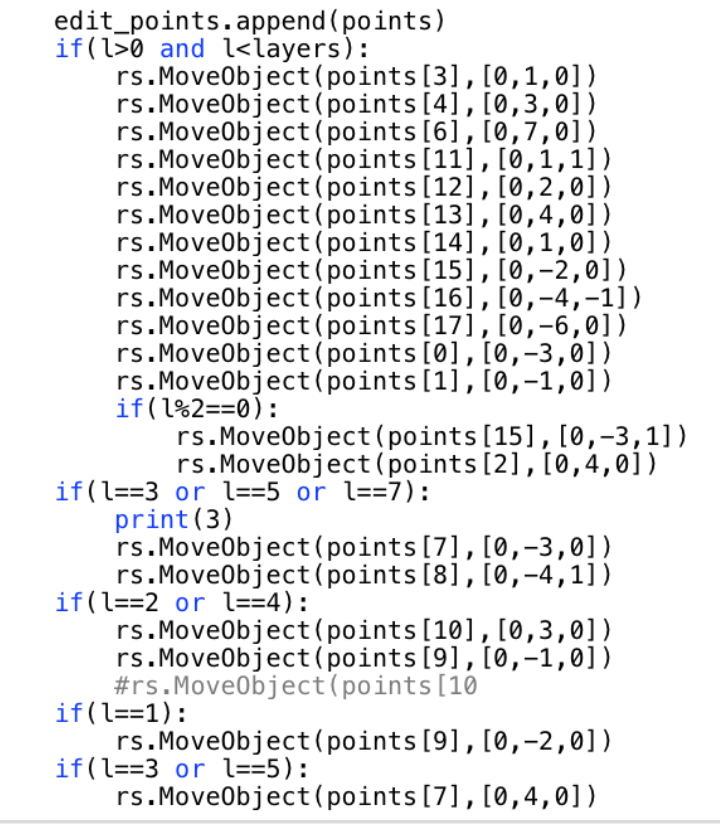
I did have a problem at first where I thought that I had to enter the coordinate to which I wanted the point to move, which was giving me really wild results. But eventually I discovered that entering 0,0,0 kept the point at its original spot, so they were following some sort of local coordinate rules.
The next program creates and tiles Metahedron’s cube, a shape from sacred geometry. This tiles as a hexagon, so I figured out how to do the hexagon tiling with the hexagon’s being drawn at the vectors with a 120 degree angle between them. Then I figured out that the shape is drawn by having six sets of two circles drawn around a center circle, with radii that are 1/4 of the vector lenght, such that the outermost circles lie on the vertices of the hexagon. Then, all center points of all circles are connected to one another.

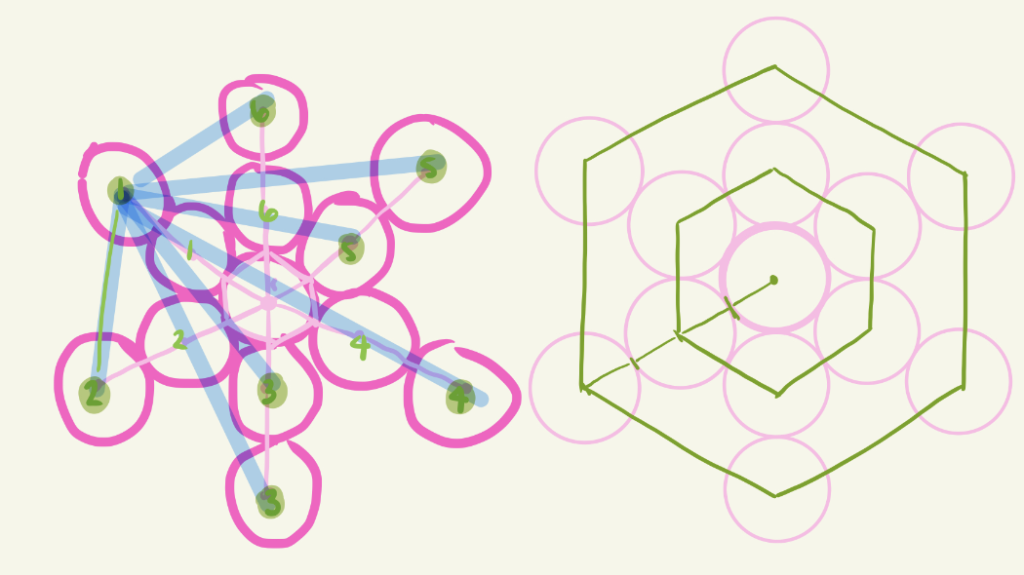
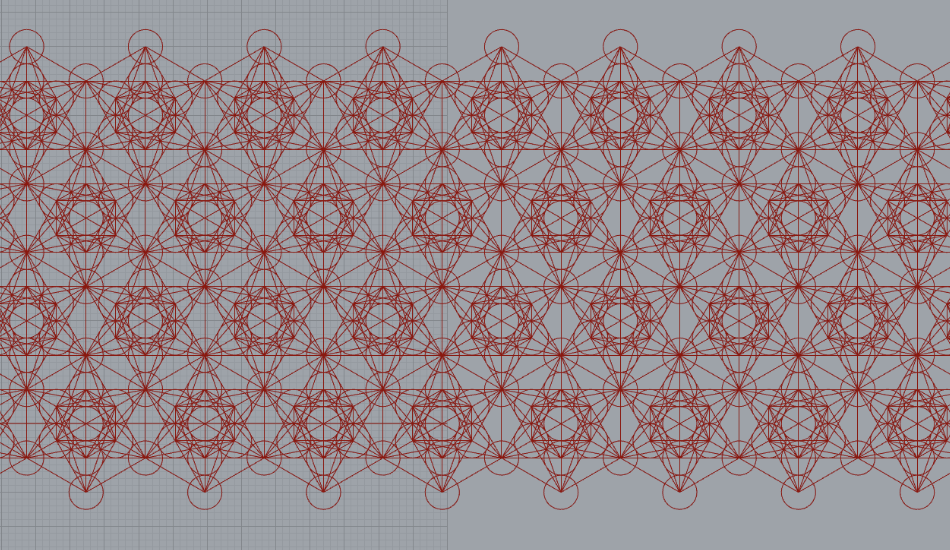
I exported the file as an svg and imported it to the GlowForge site to score the pattern on the wood. I did run into a problem where the laser head was moving the wood around. This was because I was using 3/4″ wood, but the machine can only do 1/5″ wood unless you take the crumb tray out. We did this and this time is was too low, so we found some metal blocks we could rest the wood on. Then it worked wonderfully and smelt incredible!
Next I recreated the flower of life, which I was able to make by tiling hexagons with circles draw around them with radii equal to the vector length.

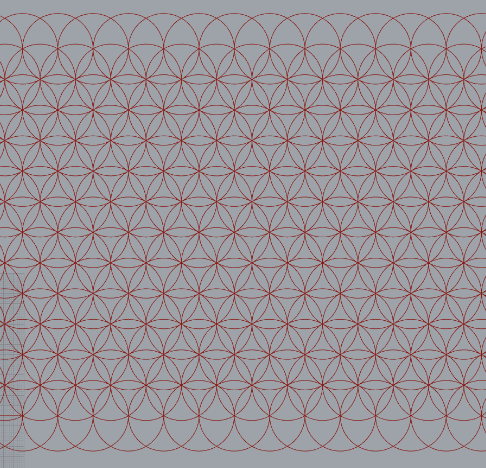

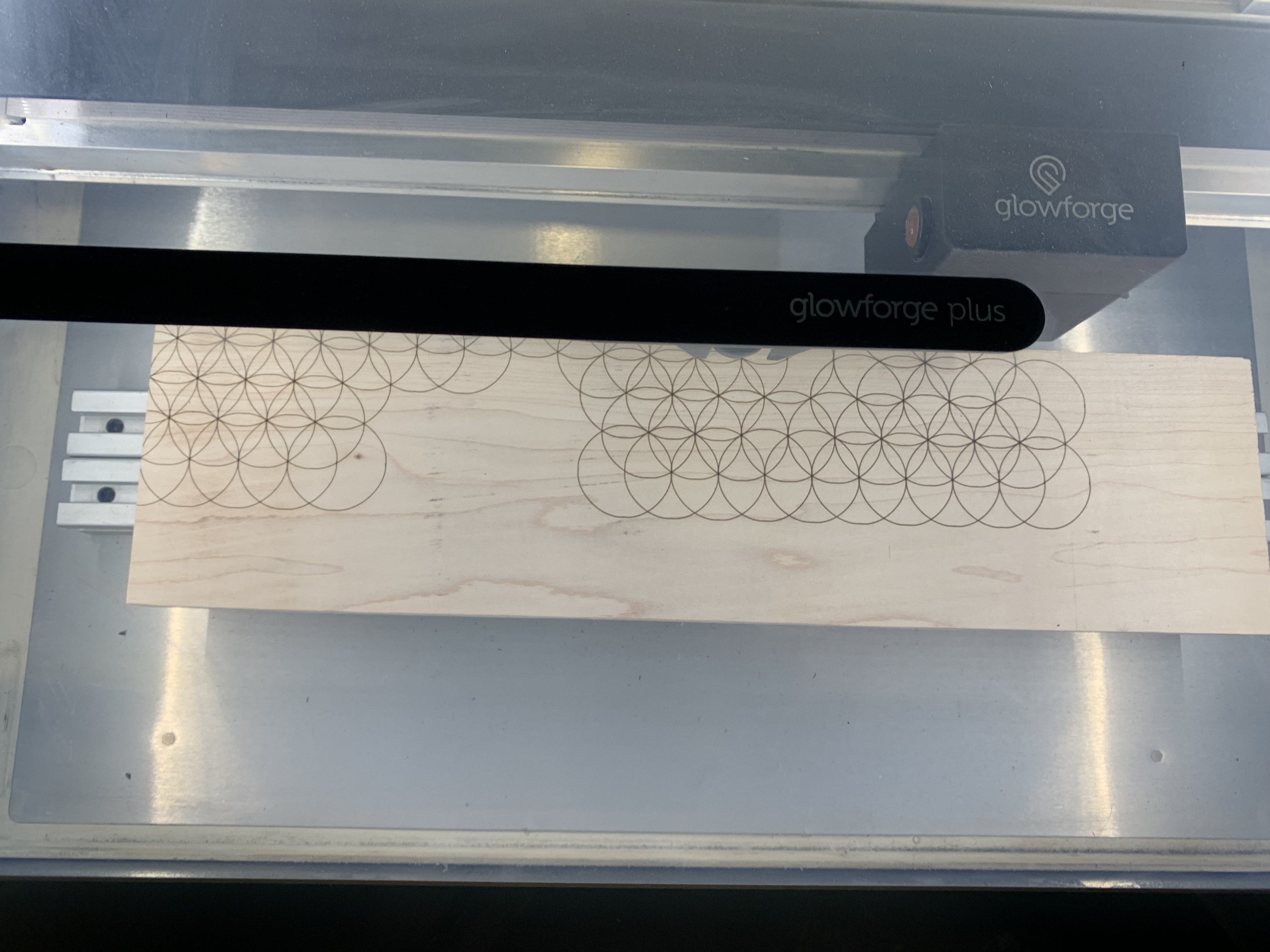
Outcome
Here is my final product. My friend Jack helped me cut out the pieces with his table saw, which was really fun to learn to use, and we glued everything together and kept everything in place with cinder blocks. The top was also carved with the CNC machine on padauk wood, and while I didn’t use computation to design it, I did use the Rhino skills that Camila taught us in class:)
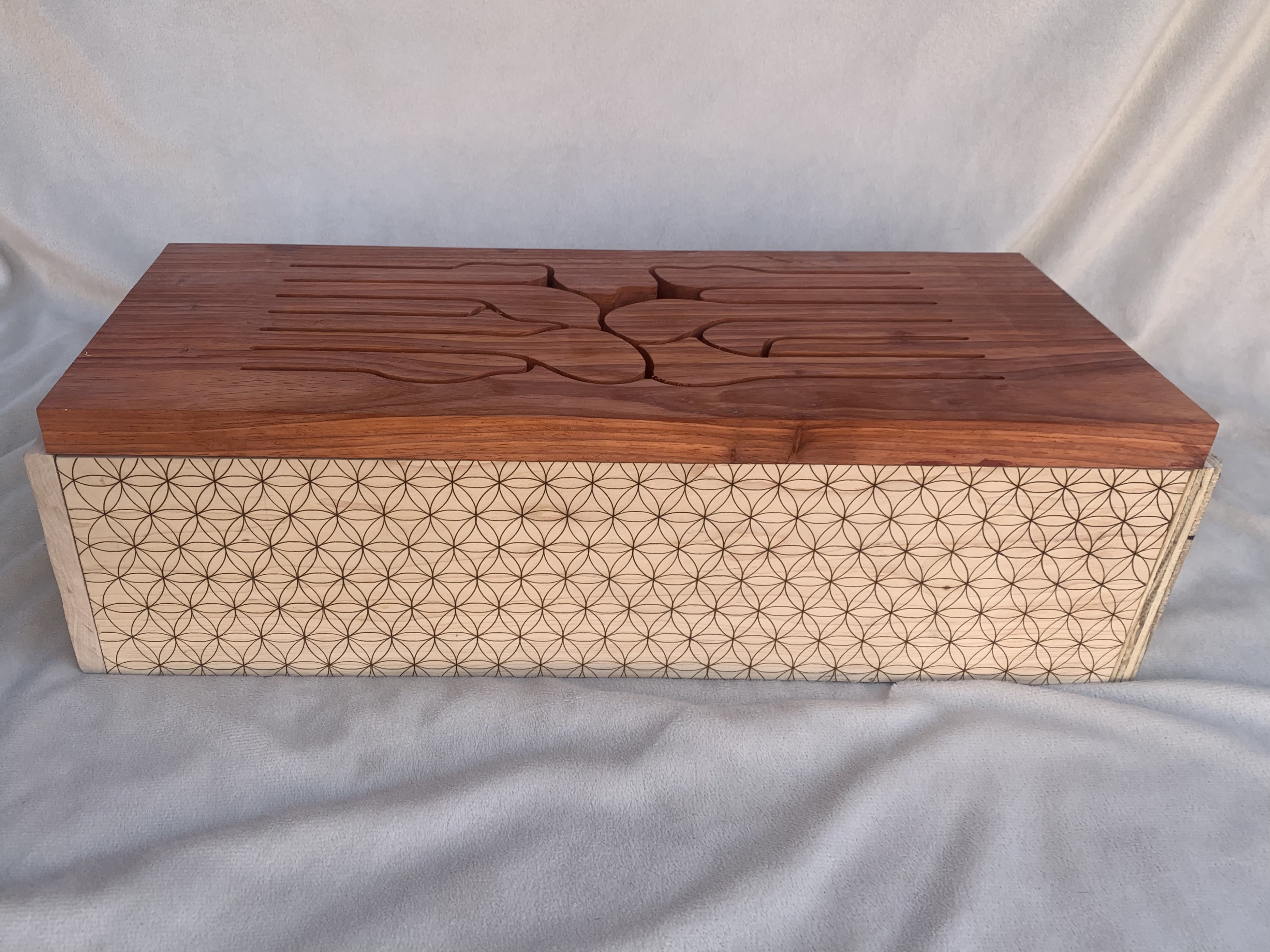
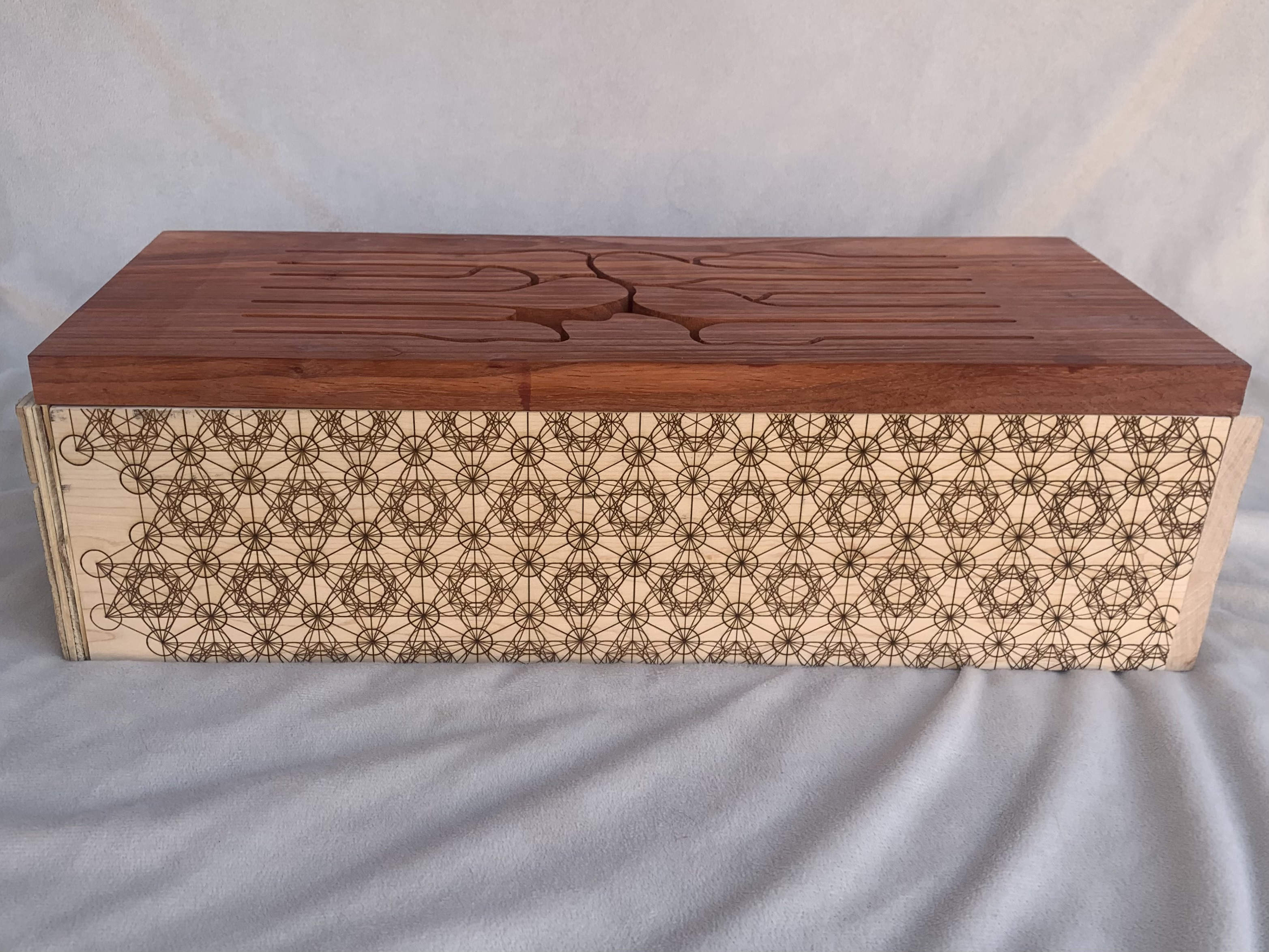

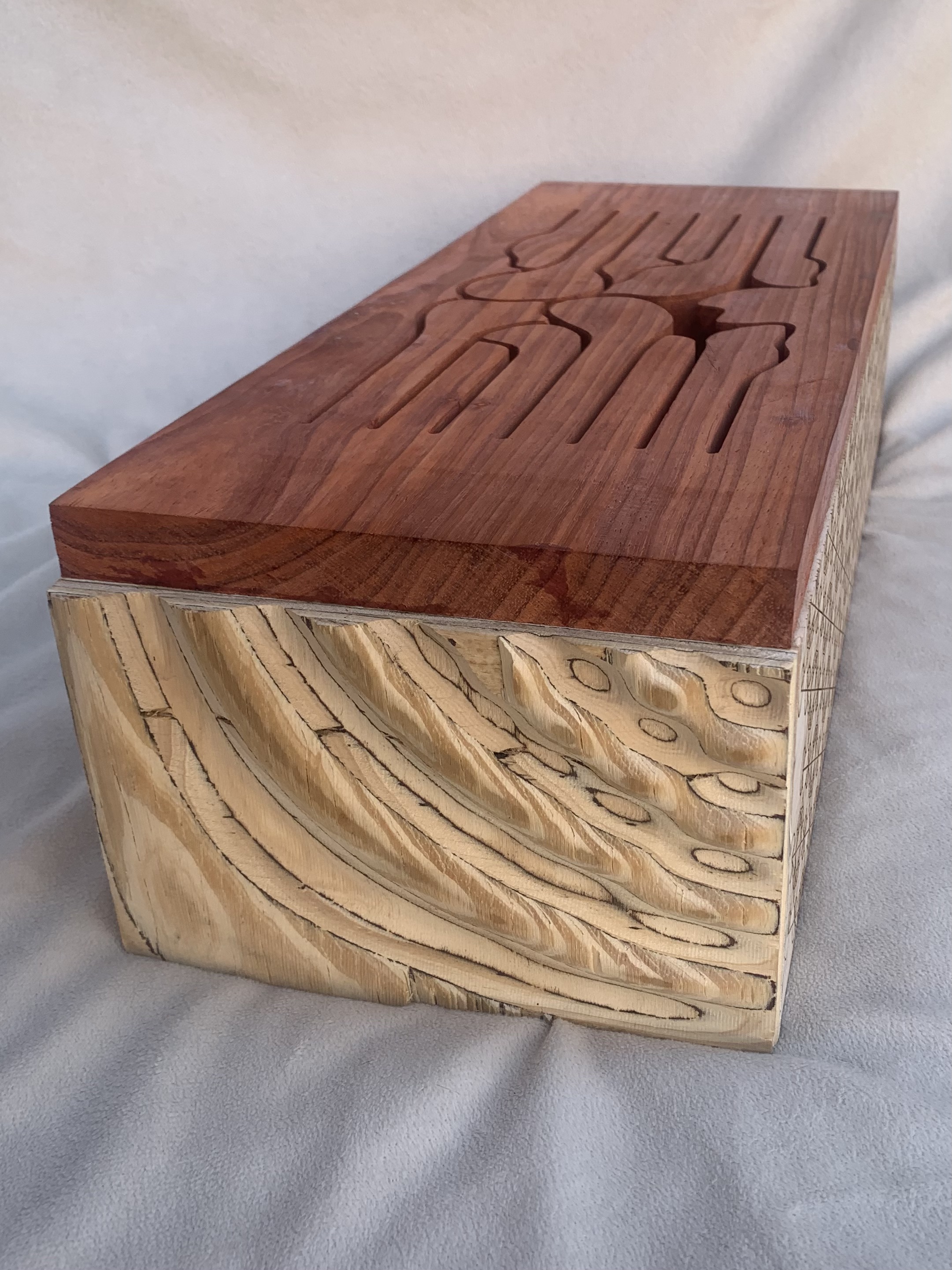

Future Work
I really like the way the plywood layers are revealed, and would like to use better plywood in the future like baltic birch. I used maple hardwood for the other sides, and I think they turned out nicely. In the future I would do more dramatic undulations for that side, as I think it’d be easier to see and reveal more of the wood grain. I also think that I would have liked to experiment with the shapes and sizes of the tongues and their sounds, as well as carving undulations or engraving designs into a piece and then carving tongues into that!
Reflection
This was a really enjoyable project. Before this class I had never really prgrammed to fulfill an idea in my head, and this project especially gave me the space and time to do that. I learned a lot about working with wood, including what types of wood work for certain situations, and how to use the CNC and GlowForge – machines for more of a subtractive fabrication approach that I hadn’t yet explored.
Code and Presentation Slides
https://docs.google.com/presentation/d/13bYkIBxCMh5qK82hZrBry0lagQUAgFTUc1_FHC75z88/edit?usp=sharing