Introduction
For my final project, I explored the creative intersection of computational design and digital fabrication by creating 3D-printed jigsaw puzzles. Inspired by our class lesson on tiling, I aimed to design and fabricate jigsaw puzzles that would challenge and delight users while showcasing the potential of computational tools. Over the course of the project, I developed multiple jigsaw puzzle cutter designs, refined a partial algorithm, and fabricated puzzles that reflect both traditional and innovative approaches to puzzle-making.
This project highlights the use of computational design to create unique puzzle patterns and leverages 3D printing technology to bring these designs to life. Below is a glimpse of the completed work:
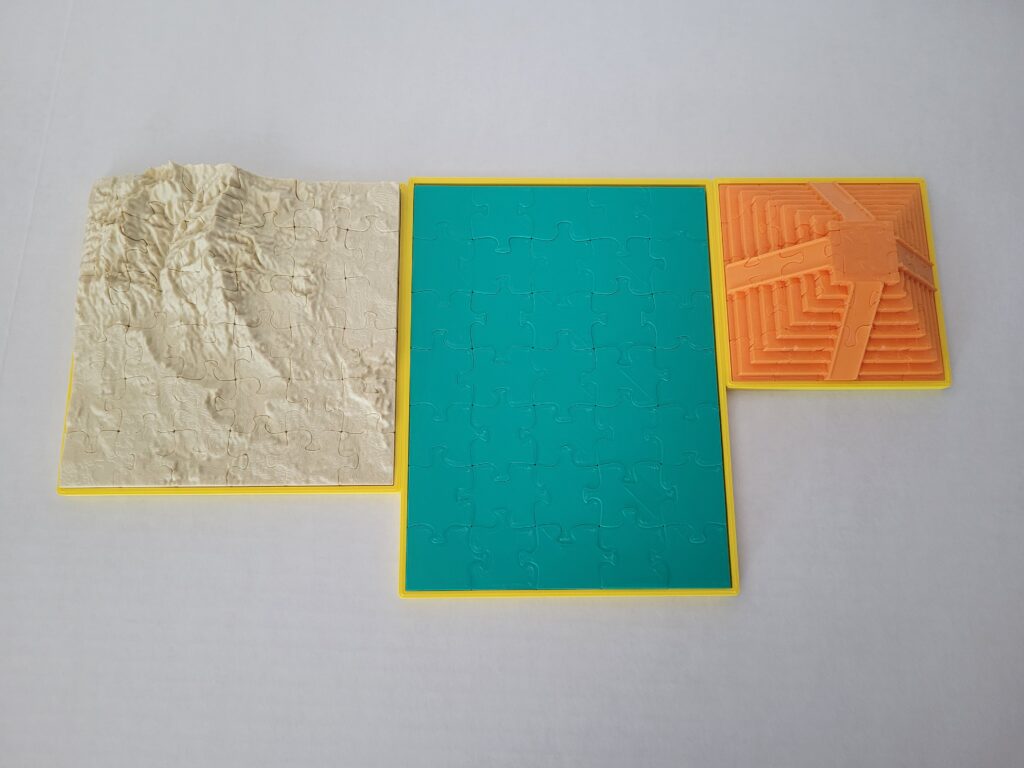
Background Research
My project builds on prior computational design research that explores interlocking and modular structures, directly influencing my approach to creating 3D-printed jigsaw puzzles. The “Design Jigsaw” framework by Chia-Hui Nico Lo et al. uses a jigsaw metaphor to organize complex ideas through interlocking visual elements, inspiring my use of parametric design to generate puzzle pieces that fit together cohesively. Similarly, the work of Gershon Elber and Myung-Soo Kim in “Synthesis of 3D Jigsaw Puzzles over Freeform 2-Manifolds” provided technical insights into designing interlocking pieces on curved 3D surfaces, which I applied to my terrain map puzzle. These studies guided my computational methods and highlighted the creative potential of algorithmic tools in fabricating interlocking designs.
Synthesis of 3D jigsaw puzzles over freeform 2-manifolds – ScienceDirect
Process
Computational Design
Puzzle Cutter Script:
I developed a grasshopper script to automate the creation of puzzle cutters by defining the cutter’s dimensions (in mm) and splitting it into rows and columns. Although I was unable to complete the algorithm for interlocking “teeth,” manual design refinements (interpret curve, join, extrude, Boolean split) in Rhino allowed me to achieve functional results.
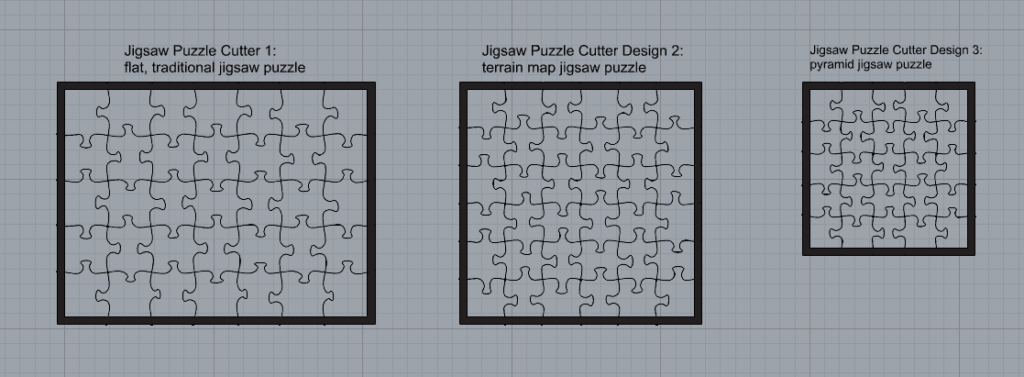
Terrain Map Puzzle:
Using GeoTIFF data, I processed elevation information in QGIS and modeled a topographic map in Rhino and Grasshopper. The map’s pixel brightness data was mapped to elevation values, generating a 3D surface that was then transformed into a puzzle. I used the same process that we learned during Week 7: Data-Driven Design
Fabrication
Each jigsaw puzzle cutter design was extruded into a 3D solid and used as a cutting tool for the base geometry. The puzzles were 3D-printed in unique colors, and yellow holders were designed to keep pieces organized.
Challenges included:
- Refining the algorithm for interlocking shapes.
- Ensuring 3D-printed pieces interlocked seamlessly without excessive post-processing.
Outcome
The final deliverables include:
- Three 3D-Printed Jigsaw Puzzles:
- Flat Puzzle (Green): Traditional design with 35 pieces, measuring 8” x 6”.
- Terrain Map Puzzle (Beige): Topographic map puzzle with 36 pieces, measuring 6” x 6”.
- Pyramid Puzzle (Orange): A pyramid jigsaw puzzle with 25 pieces measuring 4″ X 4″.
- Puzzle Holders:
Yellow holders for each puzzle to secure pieces. - Puzzle Cutter Algorithm:
A partial algorithm that defines puzzle dimensions and a grid layout, with manually completed interlocking teeth.
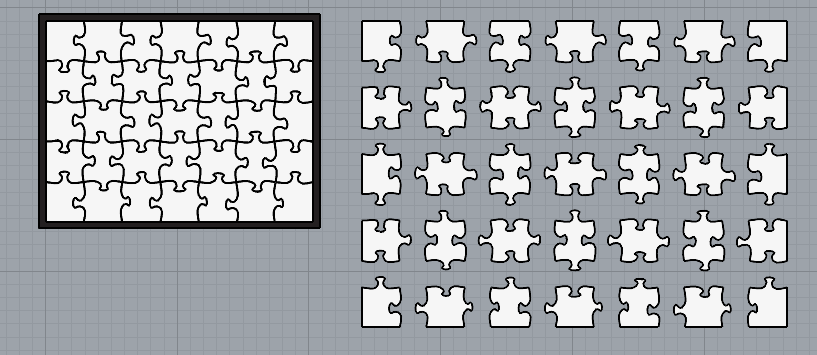
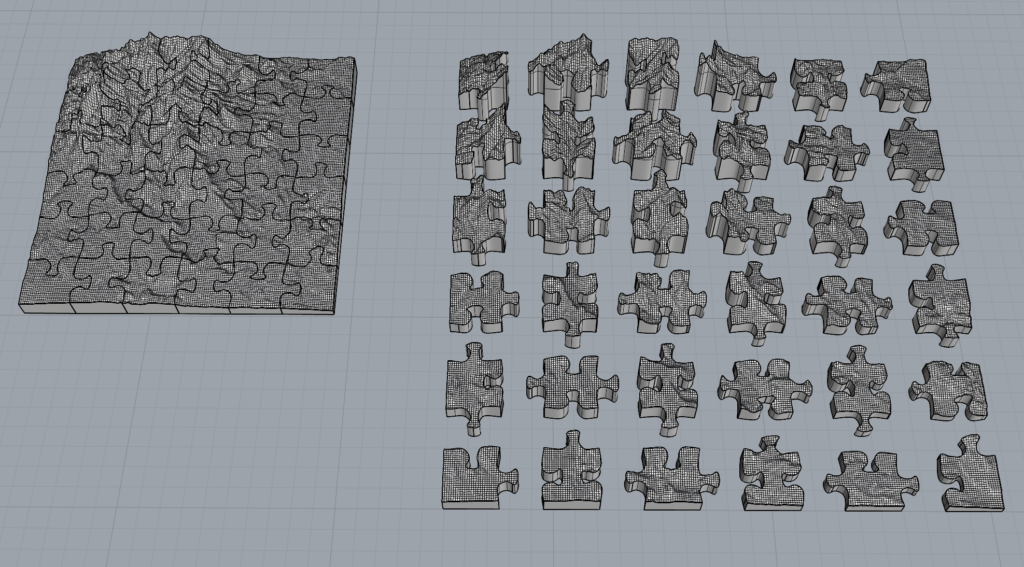
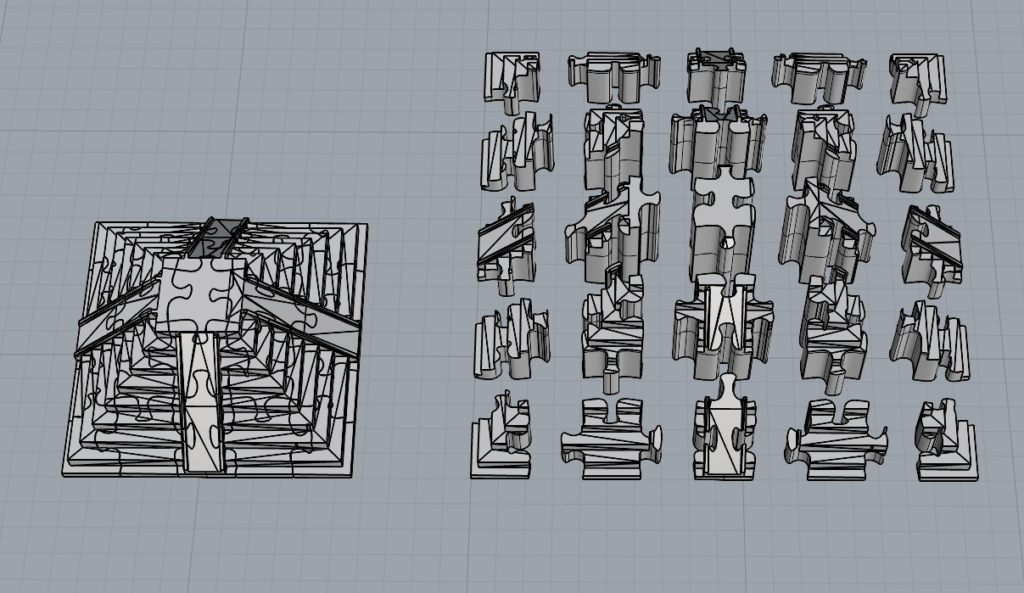
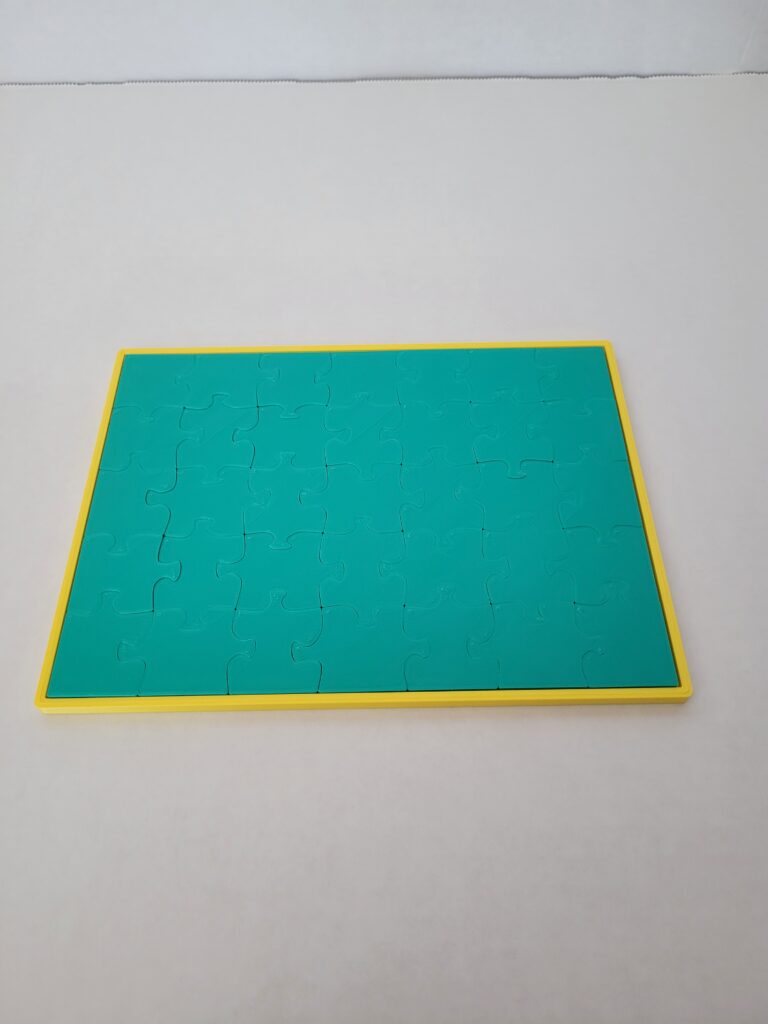
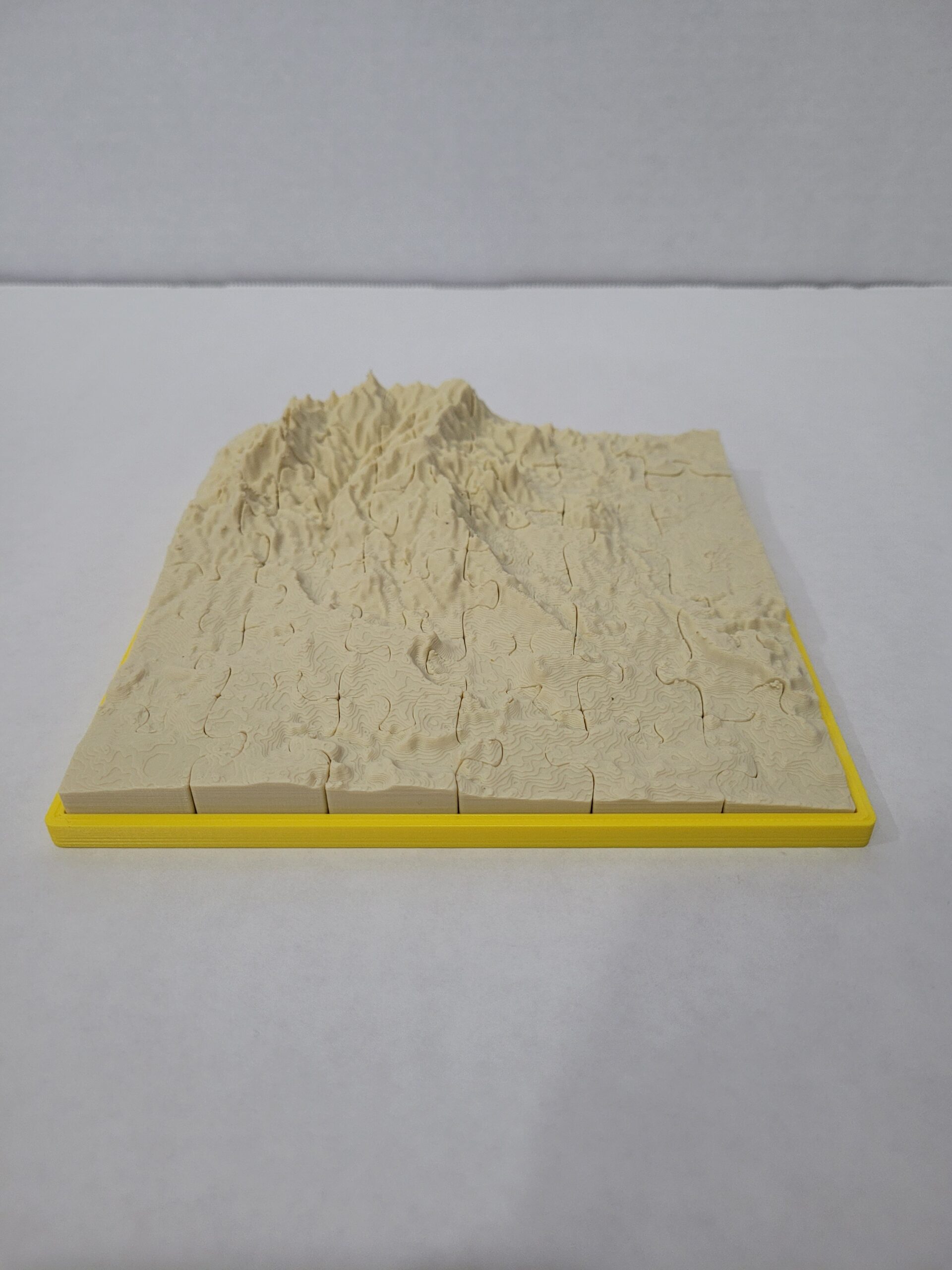
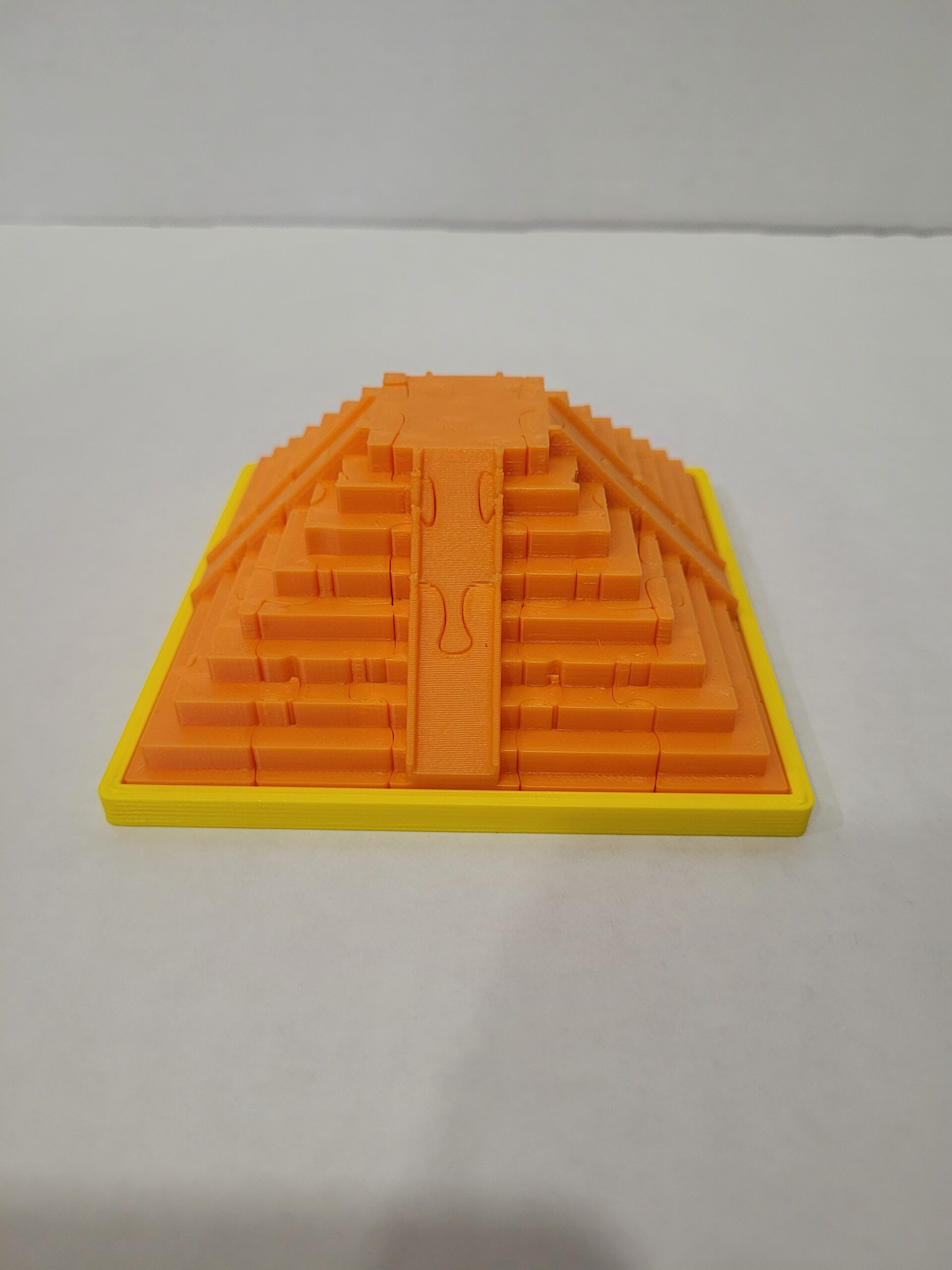
Future Work
If given more time, I would:
- Complete the algorithm to automate interlocking teeth generation.
- Experiment with multi-color or texture printing for enhanced aesthetics.
- Develop larger, more intricate puzzles to explore creative applications further.
- Experiment with different shapes for the jigsaw puzzles.
Reflection
This project deepened my understanding of computational design and fabrication. I learned how to combine algorithmic tools with manual design processes to achieve functional and creative outcomes. The jigsaw puzzles I created will serve as both functional prototypes and inspiration for future explorations in digital fabrication.
I discovered that creating these jigsaw puzzles was quite a challenge. It involved ensuring the jigsaw cutter accurately sliced the surface, monitoring the 3D printer to produce high-quality pieces, and patiently waiting for all the pieces to be printed, all while making sure everything went smoothly.